Why Iron Ore
Iron Ore Concentrate
Our Process
Future of Iron Ore
Our
PRODUCT
Why Iron Ore.
Iron ore is primarily used to create steel, which is essential for human progress; from culinary uses, electronics, surgical tools and medical equipment, architecture and construction to automotive and aerospace applications, it helps drive the world’s economy, and allows human beings to harness their innovation to actualize their wildest dreams.
Steel is completely recyclable; it can be converted into material of the same quality over and over. Recycling steel reduces emissions and environmental impact, and each recycled tonne of scrap steel saves more than 1,400 kilograms of iron ore!
Other uses of iron ore include creating powdered iron for magnets and catalysts, radioactive iron for biochemical research, iron blue used in paints, ink, cosmetics, dyeing, fertilizer, and industrial finishes, and black iron oxide – a pigment used in polishing compounds, metallurgy, medicine, and the electronics industry.
Canada exported 52.2 million tonnes of iron ore in 2019, worth roughly $6.6 billion. Pelletized iron ore accounted for 29.6% ($2.4 billion) of the volume, while the remaining 70.4% ($4.2 billion) was iron ore concentrate.
Iron Ore Premium Concentrate
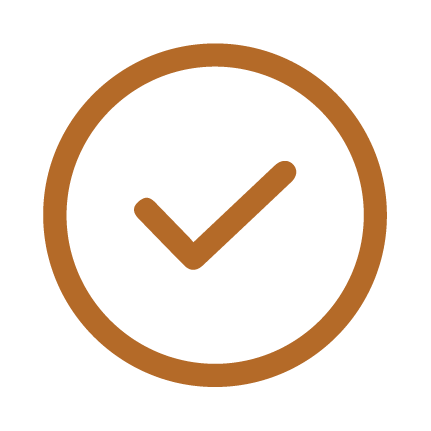
High Quality
65.5% Fe
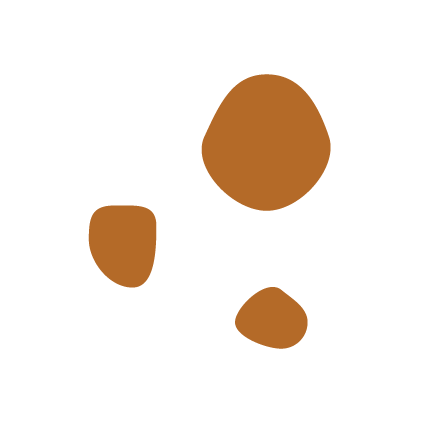
Low Impurity
Low silica and manganese content
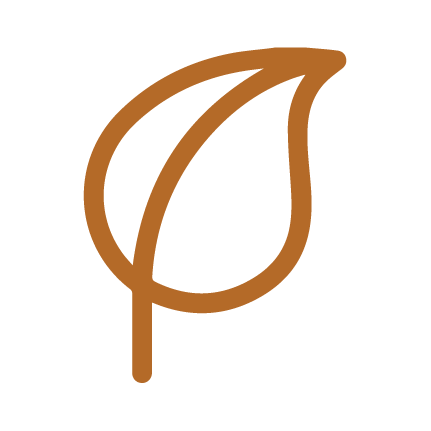
Significant Environmental Benefits
Lower Carbon Footprint per Tonne of Steel
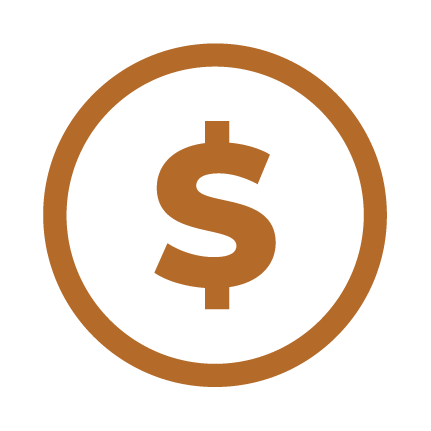
Cost Benefits
Higher Iron = Lower Transport and Processing Costs per Tonne of Steel
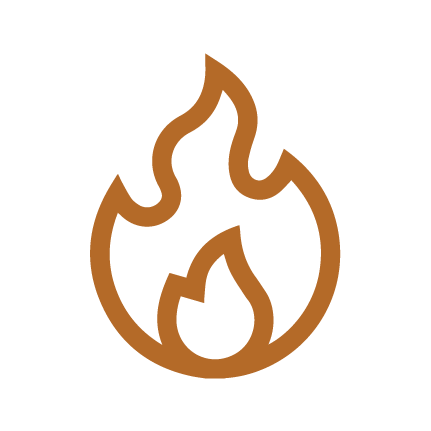
Increased Blast Furnace Productivity
Higher Recovery of Iron
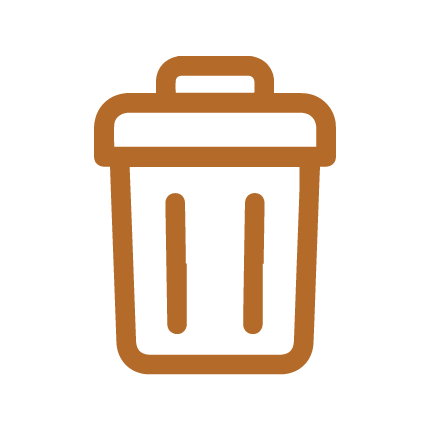
Reduced Slag Volumes
Cleaner Concentrate = Less Waste
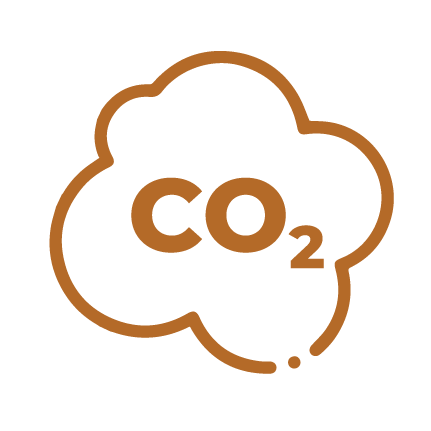
Lower CO2 Emissions
Per tonne of steel produced
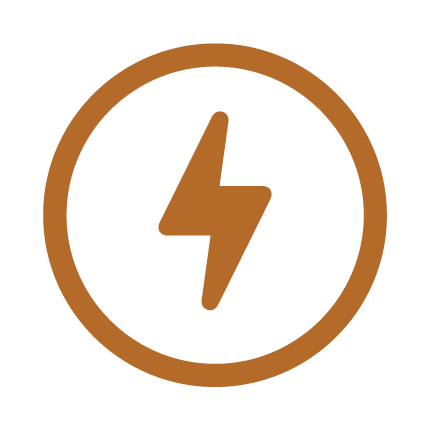
Reduced Energy Requirements
For pelletizing
Iron Ore Concentrate
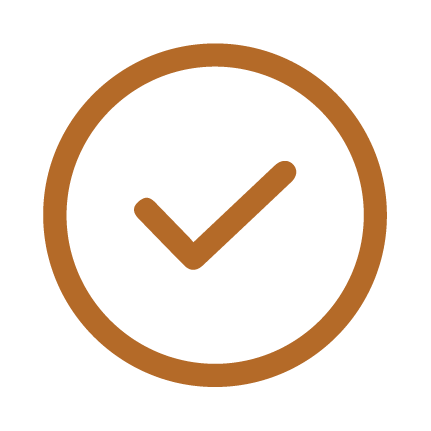
High Quality
65.5% Fe
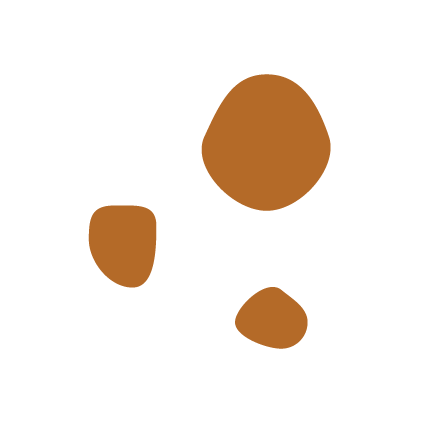
Low Impurity
Low silica and manganese content
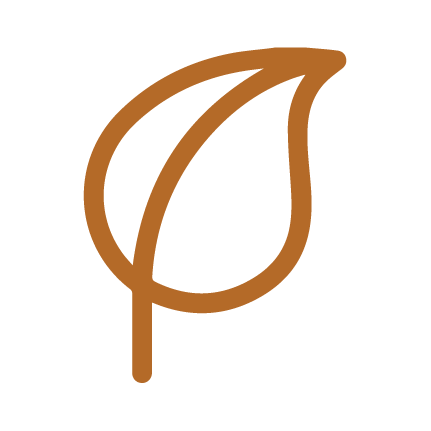
Significant Environmental Benefits
Lower Carbon Footprint per Tonne of Steel
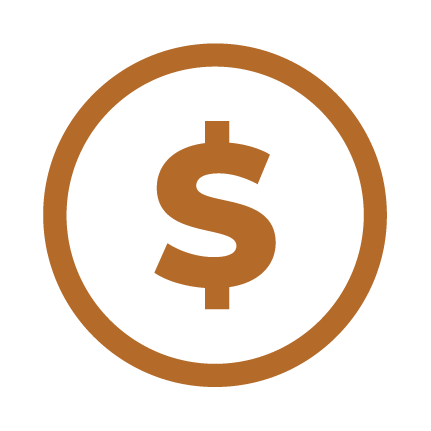
Cost Benefits
Higher Iron = Lower Transport and Processing Costs per Tonne of Steel
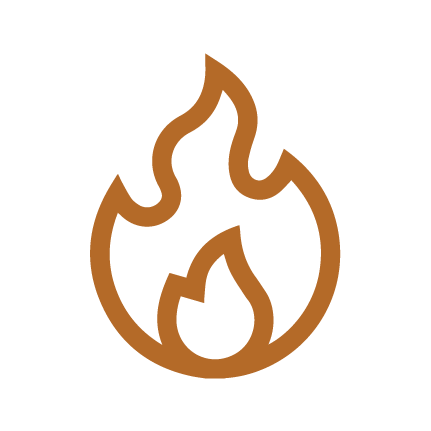
Increased Blast Furnace Productivity
Higher Recovery of Iron
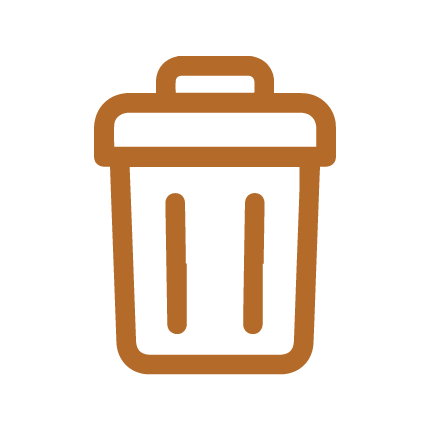
Reduced Slag Volumes
Cleaner Concentrate = Less Waste
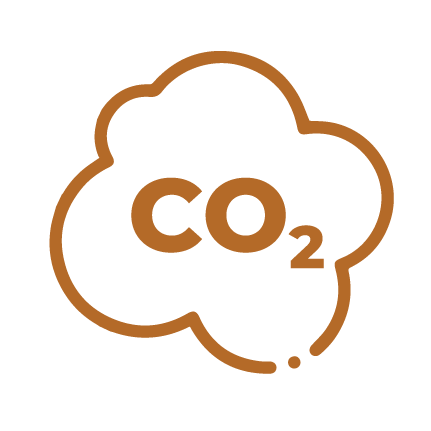
Lower CO2 Emissions
Per tonne of steel produced
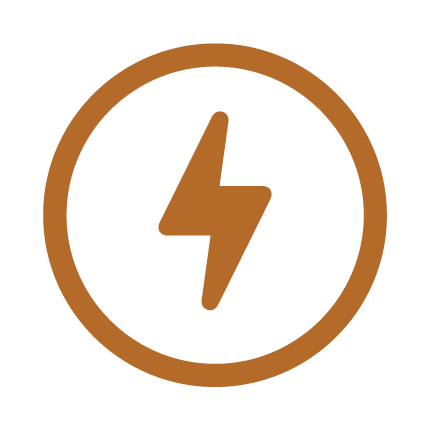
Reduced Energy Requirements
For pelletizing
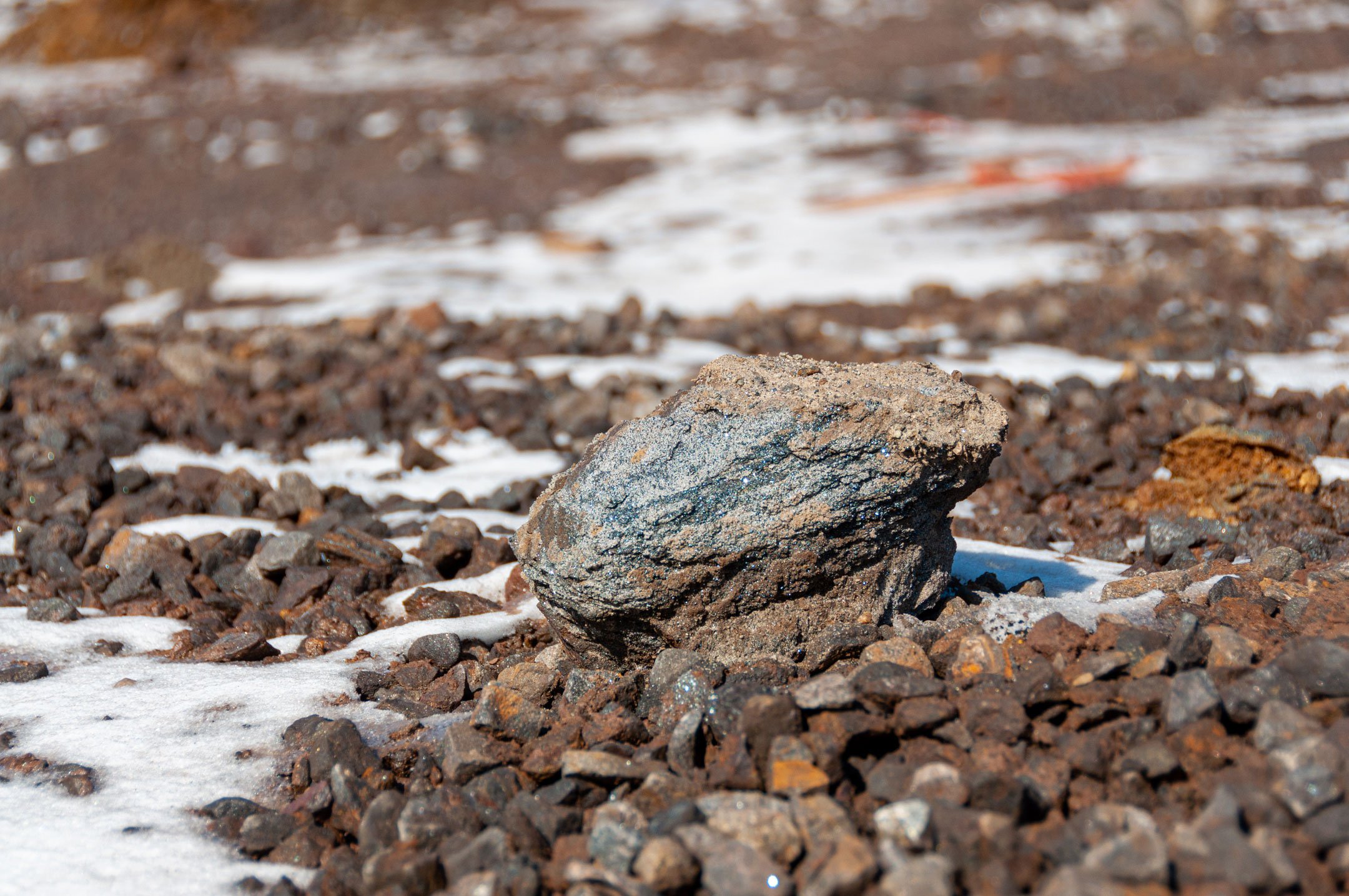
Our process.
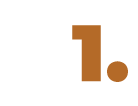
Drilling and Blasting
The blasting team prepares the designated area for mining to break up the rock and facilitate ore extraction.
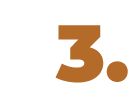
Iron Ore Is Crushed
Large raw material is crushed into smaller material to be processed in the mill.
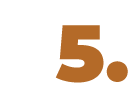
Drying Process
The high-grade iron ore is dried to remove all moisture prior to shipping.
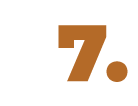
Train Loading
High-quality, dry iron ore is loaded onto a train and transported to port for shipping.
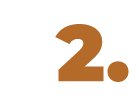
Heavy Equipment Operation
Heavy equipment is used to mine and haul iron ore from the pit to the crusher.
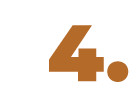
Iron Separation
After leaving the mill, iron ore is sent through the spirals where water and gravity are used to separate the heavier iron ore from the lighter impurities.
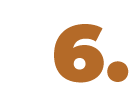
High-Tension Magnetic Removal Process
The dried iron ore is put through the high-tension magnetic process to remove final impurities.
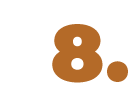
High-Efficiency Steel Production
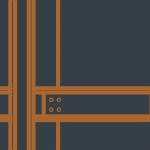
Iron ore is shipped to steel producers where low-waste steel is fabricated and used globally.
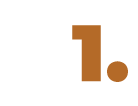
Drilling & Blasting
The blasting team prepares the designated area for mining to break up the rock and facilitate ore extraction.
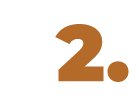
Heavy Equipment Operation
Heavy equipment is used to mine and haul iron ore from the pit to the crusher.
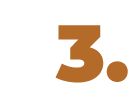
Iron Ore Is Crushed
Large raw material is crushed into smaller material to be processed in the mill.
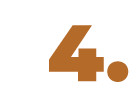
Iron Separation
After leaving the mill, iron ore is sent through the spirals where water and gravity are used to separate the heavier iron ore from the lighter impurities.
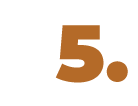
Drying Process
The high-grade iron ore is dried to remove all moisture prior to shipping.
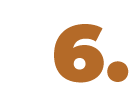
High-Tension Magnetic Removal Process
The dried iron ore is put through the high-tension magnetic process to remove final impurities.
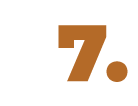
Train Loading
High-quality, dry iron ore is loaded onto a train and transported to port for shipping.
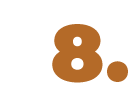
High-Efficiency Steel Production
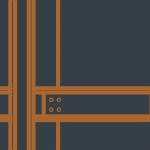
Iron ore is shipped to steel producers where low-waste steel is fabricated and used globally.
The Future of Iron ore
We are meeting the world’s need for sustainable iron ore.
As global demand for iron ore continues to rise, numerous factors are shaping the industry’s future. External disruptions and supply uncertainties contribute to market volatility, while governments worldwide are introducing new decarbonization initiatives. Resource companies must now focus on adopting innovative mining processes, enhancing operational efficiency, and reducing fuel consumption while continuing to enhance health and safety, reduce accidents, and address ergonomic risks within our operations. Our goal is to lower costs, improve employee well-being, and boost profitability by adapting to the evolving market landscape.
Emerging technologies, such as AI and drones, will play a crucial role in this transformation. Although the shift toward decarbonization and electric arc furnace (EAF) production may reduce iron ore demand, the need for high-quality ore remains significant. Additionally, factors such as pricing mechanisms, high-grade ore trends, market dynamics, trade flows, and the development of China’s steel industry will influence the market. We are committed to preparing for these challenges and seizing opportunities as they arise.
Cleaner concentrate = less waste, reducing the environmental impact associated with slag disposal, such as landfilling or reprocessing, helping Tacora achieve more sustainable operations.
High-grade Ore.
As a leader in the green steel revolution, Tacora’s highgrade, low-silica iron ore is produced with a strong commitment to sustainability, surpassing the world’s most stringent environmental standards. This premium ore enhances the effi ciency of steel production, which is foundational to modern technological advancements and infrastructure development worldwide. Iron ore’s primary use is in steelmaking—a material crucial to global progress. Steel’s versatility extends from kitchen appliances and electronics to medical instruments, architecture, automotive, and aerospace industries, fueling economic growth and enabling human innovation.
Manganese
Manganese is a by-product of iron ore production. As Tacora extracts and processes iron ore, manganese is separated out and collected as a secondary product.
Tacora Resources has received funding from ACOA, with the allocation of $1.25M in a repayable loan, to help with the planning and development of a Manganese Sulfate Purification Plant. What was once an impediment in iron ore could now be the future of the green economy as the auto sector electrifies and we continue to decarbonize.
Manganese sulfate plays a critical role in decarbonization, primarily through its use in the production of batteries for electric vehicles (EVs) and energy storage systems. As a key component in lithium- ion batteries, manganese sulfate enhances the stability and efficiency of battery cathodes, which are essential for longer-lasting and safer batteries. The growth of the EV market and renewable energy storage solutions directly ties manganese sulfate to the transition to cleaner energy and reduced carbon emissions. Additionally, manganese sulfate is used in fertilizers, which are vital for sustainable agriculture. By improving crop yields and soil health, it supports environmentally friendly farming practices that are essential for feeding a growing global population while minimizing the environmental impact of agriculture.
With its vast supply of rich manganese tailings, Tacora Resources is working on a plan to become a major contributor to the critical mineral supply chain that will play a vital role in the electrification of the auto industry.
Manganese sulfate contributes to the green economy by enabling advancements in energy storage, electric transportation, and sustainable agriculture, all of which are crucial for reducing greenhouse gas emissions and promoting sustainability.