Our Approach
Health & Safety
Emergency Response
Environment
Community Relations
Local Impact
Indigenous Relations
Reports & Policies
SUSTAINABILITY
Our Approach
Our Key Beliefs at Tacora (Guiding Principles)Ā
We believe that all injuries and fatalities are preventable. We believe in a culture where the health and safety of all workers is an overriding value. We believe that excellence in health and safety is important to our long-term success.Ā
Shared ResponsibilityĀ
We are collectively and individually responsible for the safety of all workers and all worksites. Individuals must assume responsibility for their own safety and co-workersā safety by following all safety rules, procedures, and practices, refusing to perform unsafe work, and taking collective responsibility for othersā unsafe conduct. Contractors must also take a leadership role in ensuring worker health and safety and assuring accountability for safety on the worksite.Ā
Commitment to TrainingĀ
We understand the importance of workers being fully prepared for the work they do. All workers on our worksite must be competent and fully trained and certified for the work they are performing.Ā
Continual Improvement
We are committed to the on-going improvement of our practices and support efforts to develop and implement new methods, procedures, and technologies that have the potential to improve safety. We actively engage our workforce to provide feedback and improvement initiatives.Ā
Recognition of Safety Performance and PracticesĀ
The commitment to health and safety is to all workers, not just direct employees. When engaging contractors, sub-contractors, and others to provide services, the selection process and administration of contracts include recognition and support of good safety performance and practices.Ā
Leadership
Our leaders uphold our beliefs, values, and standards. Our leaders never walk past an unsafe activity or workplace condition without taking action. Our leaders believe in leading by example, and actively engage our workforce to provide feedback and improvement initiatives.
Read our sustainability progress report in detail.
Health and Safety
At Tacora, we strive to eliminate all hazards and risks to our workersā health. To accomplish this, occupational hygiene risk assessments and findings are carried out through monitoring and exposure controls, which protect all our employeesā health. Ā We also have a Primary Care Paramedic as well as trained Advanced Medical First Responders onsite at all times.Ā Ā
To learn more about safety and our protocols, click here.
We also recognize that the most common occupational diseases are hearing loss and respiratory illness. To mitigate occupational disease instances, programs have been implemented to monitor and assess employees for exposure, and controls have been put in place. The main programs implemented, among others, have been the hearing conservation and respiratory protection programs. The hearing conservation and respiratory protection programs include medical assessments conducted on a prescribed schedule by qualified off-site medical personnel. The medical assessments are comprised of chest x-rays and miner medicals. Miner medicals provide a means of monitoring our employeesā wellness, including their hearing and lung health. As a result, appropriate measures can be taken to safeguard against exposure and irreversible damage to employeeās health.
This year, we have enhanced our Emergency Response Team (ERT) to bolster safety and preparedness. This team focuses on improving rapid response to onsite incidents, including mine-specifi c emergencies. Tacora’s ERT includes trained personnel ready to handle a range of situations, from medical emergencies to mine rescues, ensuring a higher standard of safety for workers. The commitment to safety aligns with Tacoraās broader strategy of zero-harm, risk management, and workplace safety. We have continuously emphasized that empowering employees with emergency skills and resources is crucial for maintaining a safe and healthy work environment.
Health and Safety
At Tacora, we strive to eliminate all hazards and risks to our workersā health. To accomplish this, occupational hygiene risk assessments and findings are carried out through monitoring and exposure controls, which protect all our employeesā health. Ā We also have a Primary Care Paramedic as well as trained Advanced Medical First Responders onsite at all times.
To learn more about safety and our protocols, click here.
We also recognize that the most common occupational diseases are hearing loss and respiratory illness. To mitigate occupational disease instances, programs have been implemented to monitor and assess employees for exposure, and controls have been put in place. The main programs implemented, among others, have been the hearing conservation and respiratory protection programs. The hearing conservation and respiratory protection programs include medical assessments conducted on a prescribed schedule by qualified off-site medical personnel. The medical assessments are comprised of chest x-rays and miner medicals. Miner medicals provide a means of monitoring our employeesā wellness, including their hearing and lung health. As a result, appropriate measures can be taken to safeguard against exposure and irreversible damage to employeeās health.
This year, we have enhanced our Emergency Response Team (ERT) to bolster safety and preparedness. This team focuses on improving rapid response to onsite incidents, including mine-specifi c emergencies. Tacora’s ERT includes trained personnel ready to handle a range of situations, from medical emergencies to mine rescues, ensuring a higher standard of safety for workers. The commitment to safety aligns with Tacoraās broader strategy of zero-harm, risk management, and workplace safety. We have continuously emphasized that empowering employees with emergency skills and resources is crucial for maintaining a safe and healthy work environment.
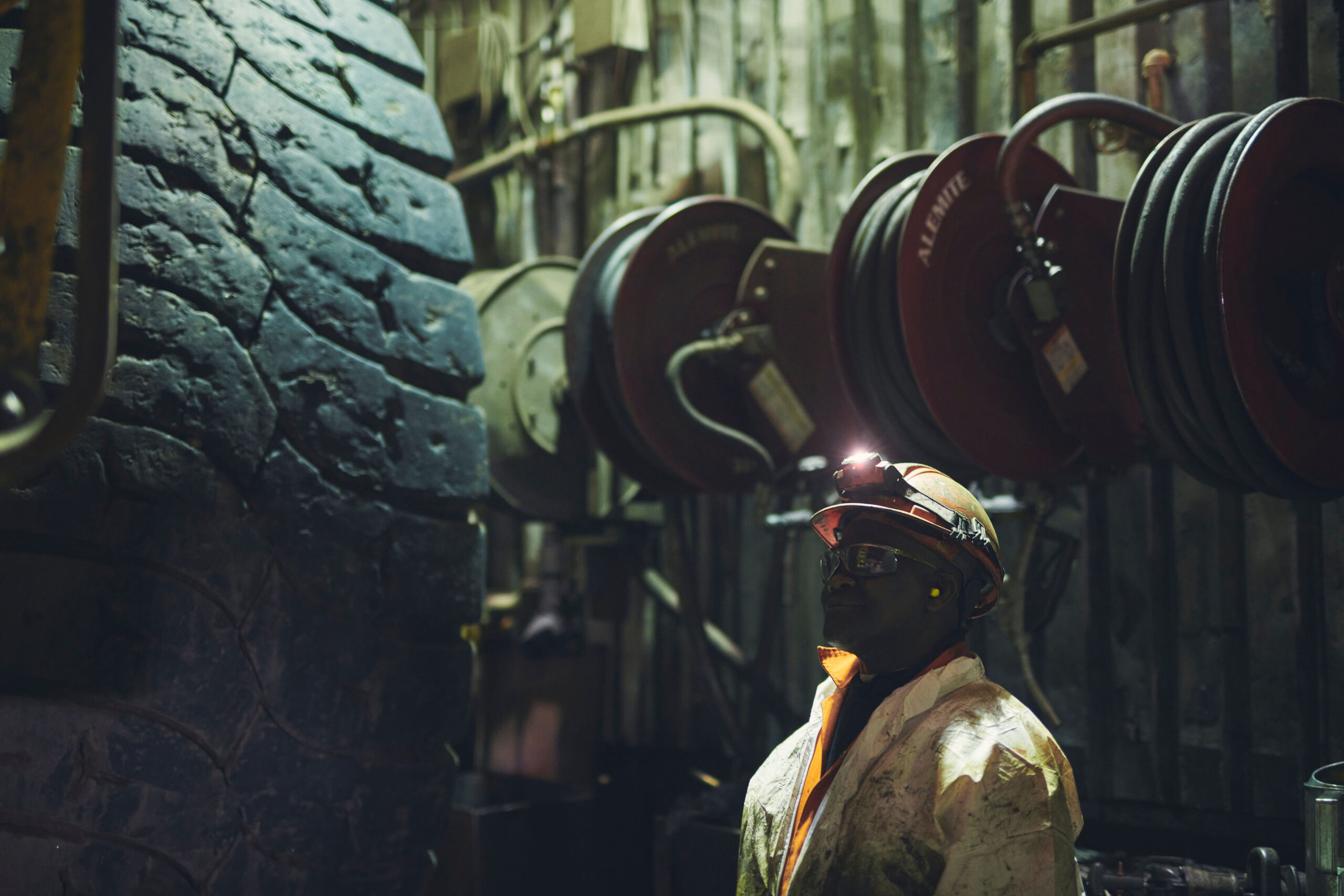
Emergency Response
Tacora values the implementation of the Companyās Emergency Response Plan (ERP) and has developed measures to safeguard personnel onsite, the environment, community, and property and assets.
The ERP ensures that a necessary emergency preparedness level is available and used as a guidance document for the Tacora operations. The plan was based on an assessment undertaken to identify the types of reasonably foreseeable emergencies, and comprehensive plans developed to support those emergencies.
Our emergency response plans are reviewed regularly, and ERP training has been provided for employees and leaders.
We work very closely with the local Fire Department and have a secured Mutual Aid Agreement in place. Volunteers of the local Fire Department have been on site to become familiar with the business areas, location of fire suppression system and equipment.
Emergency Response
Tacora values the implementation of the Companyās Emergency Response Plan (ERP) and has developed measures to safeguard personnel onsite, the environment, community, and property and assets.
The ERP ensures that a necessary emergency preparedness level is available and used as a guidance document for the Tacora operations. The plan was based on an assessment undertaken to identify the types of reasonably foreseeable emergencies, and comprehensive plans developed to support those emergencies.
Our emergency response plans are reviewed regularly, and ERP training has been provided for employees and leaders.
We work very closely with the local Fire Department and have a secured Mutual Aid Agreement in place. Volunteers of the local Fire Department have been on site to become familiar with the business areas, location of fire suppression system and equipment.
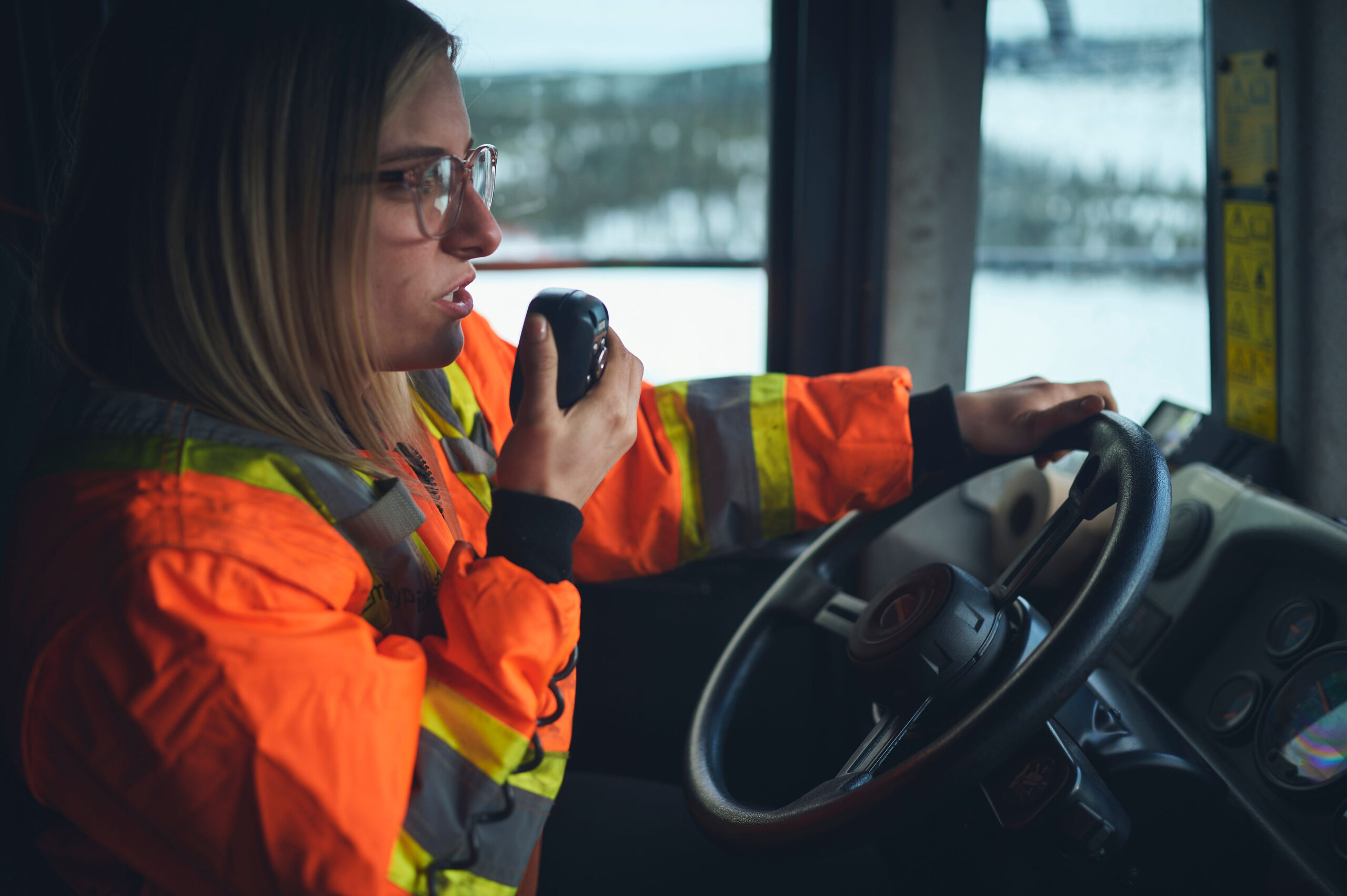
Environment
Water
Water management is a critical aspect of Tacoraās sustainable mining practices, as water plays a vital role in both mining and mineral processing operations. Recognizing the importance of this shared resource, Tacora ensures that water used in its operations is responsibly managed and discharged back into the natural environment in compliance with regulatory standards.
Tacora proactively addresses potential water-related impacts, including water availability, ecosystem value, and community needs. Comprehensive water quality monitoring procedures are in place to detect changes in water quality or aquatic biodiversity resulting from operational activities.
MONITORING AND COMPLIANCE
Tacora conducts routine effluent and water quality monitoring at specified intervalsāweekly, monthly, and quarterlyāas mandated by federal and provincial regulations, including the Metal and Diamond Mining Effluent Regulations and the provincial Certificate of Approval. Monitoring involves:
- Sampling at Final Discharge Points (FDPs), including locations such as Flora Lake and KnollĀ Lake Discharge.
- Field measurements of pH, temperature,Ā effluent velocity, and depth for accurate volume calculations.
- Laboratory testing for parameters such as metals, suspended solids, radium-226, un-ionized ammonia, and hydrocarbons, as well as acute and sublethal toxicity.
Results are reported to regulatory agencies, ensuring transparency and accountability in effluent quality.
Ā
EXPANDED SAMPLING FRAMEWORK
Tacoraās water quality assessments extend beyond FDPs to include environmental exposure and reference areas. Twelve monitoring sitesāsuch as Flora Outlet Arm, Wabush Narrows, Long Lake, Walsh River, and Jean Riverāare visited quarterly. These sites provide data on water quality across operational, reference, and environmental effects monitoring zones.
0m3
Municipal Water Used
Climate Change
Tacora is fully committed to reducing emissions to mitigate the climate change impacts of its operations. This commitment begins with setting practical, science-based targets to ensure accountability in achieving these goals. Tacora is proactively developing a long-term emissions reduction strategy aimed at achieving a 12% reduction in GHG emission intensity. The calculated GHG emissions intensity in 2023 demonstrated a 13% reduction from stationary combustion and electricity generation and an 11% reduction from mobile transportation and blasting, compared to 2022 levels.
The path to measurable emission reductions is defined by:
- Calculating annual GHG emission inventories;Ā
- Identifying areas where mitigative measures are impactful and feasible;Ā
- Pursuing opportunities and technology that improve efficiencies as well as reduce energy consumption and GHG emissions;Ā
- Collaborating internally and externally on policies and regulations; andĀ
- Reevaluating our approach as technologies, goals, and circumstances change.
Industrial Hygiene
As part of Tacoraās Health, Safety, and Environment program, industrial hygiene plays a crucial role in protecting employee health and well-being. Workplace hazards, including physical, chemical, ergonomic,āā and biological agents, can lead to acute injuries and long-term chronic effects if not addressed. Tacora focuses on proactively identifying, monitoring, and reducing these exposures to minimize risks and prevent occupational diseases.
The companyās industrial hygiene programs assess potential risks specific to operational areas and work groups, using the hierarchy of controls to mitigate exposures effectively. Comprehensive procedures and monitoring systems have been implementedĀ to manage and control these hazards,Ā ensuring a safer workplace for all employees. These efforts highlight
Tacoraās commitment to prioritizingĀ health and safety in all aspects of its operations.
Tailings Management
Tacoraās Rehabilitation and Closure Plan (RCP) focuses on progressive rehabilitation of tailings, including an annual revegetation program to keep pace with tailings surface expansion. The Tailings Impoundment Area (TIA), used for waste storage, can generate dust clouds affecting nearby communities and ecosystems. To address this, Tacora implements dust suppression and revegetation, cultivating dense plant growth to form a living dust barrier that supports biodiversity and creates habitats for local wildlife.
In 2023, Tacora revegetated 25 hectares of tailings, emphasizing native species and ecosystem restoration. Flora Basin, used for tailings since 1965, spans 1,250 hectares. By 2016, 868 hectares had been vegetated as part of a remediation program. After the mine reopened in 2018, incremental revegetation replaced full-scale remediation, targeting inactive areas for ecological restoration.
Tacoraās progressive rehabilitation focuses on reducing dust emissions and expanding ecosystems to create habitats for beneficial organisms. In 2023, 22 of 25 hectares were revegetated using hydroseeding. SEM Ltd., Tacoraās environmental consultant, conducted trials with various mulches and additives to optimize vegetation growth under site-specific conditions.
Profileās HP-wood mulch and Proganics, a product designed to enrich soil with organic matter and microbial life, were the primary mulches. Pelletized chicken manure was used as a slow-release fertilizer to sustain nutrients while minimizing leaching risks. For two hectares,
an ATV with a spreader and custom incorporator
was used, applying fertilizer and seed blends directly onto the tailings surface. This approach demonstrated innovative methods to adapt rehabilitation to the unique challenges of the site.
One of the 25 hectares designated for re-vegetation was completed through the hand planting of beach grass culms or stems. Given the unique biology
of American beach grass, Tacoraās environmental consultant opted for this method to avoid the challenges associated with growing the species from seed, ensuring more successful establishment and growth.
Key insights from 2023 revealed that tailings conditions are unsuitable for healthy plant growth without major intervention. To establish a thriving ecosystem, Tacora adopted a blended strategy combining hydroseeding, mechanical incorporation, and hand planting. Over
700 seedlings and saplings were planted in patterns designed to support wildlife and reduce wind erosion.
Additional biodiversity enhancements included installing 20 bird nesting boxes, successfully used by Tree Swallow pairs, and adding rodent and insect habitats using alder and willow branch piles. Early 2024 results show strong, diverse growth taking root, demonstrating the strategy’s effectiveness in ecosystem restoration.
Community Relations
At Tacora, we are committed to supporting our local communities and aim to make a positive and lasting impact by contributing to the sustainability and prosperity of the communities in which we operate. Tacoraās continued mission is to develop long-term lasting sustainable relationships built on shared values and common goals.
We believe that being socially responsible is essential to our operating and financial success. We are committed to developing relationships based on open and honest communication with our stakeholders and communicating with them in a timely manner. We highly value community engagement and work continuously to maintain our license to operate. Our goal is to maximize the benefits of mining while minimizing any negative consequences from our activities.
Our operations regularly engage with community stakeholders to incorporate their values and concerns into our business activities. Our engagement programs and activities include formal and informal communication and feedback sessions; community partnerships; sponsorships and community investments.
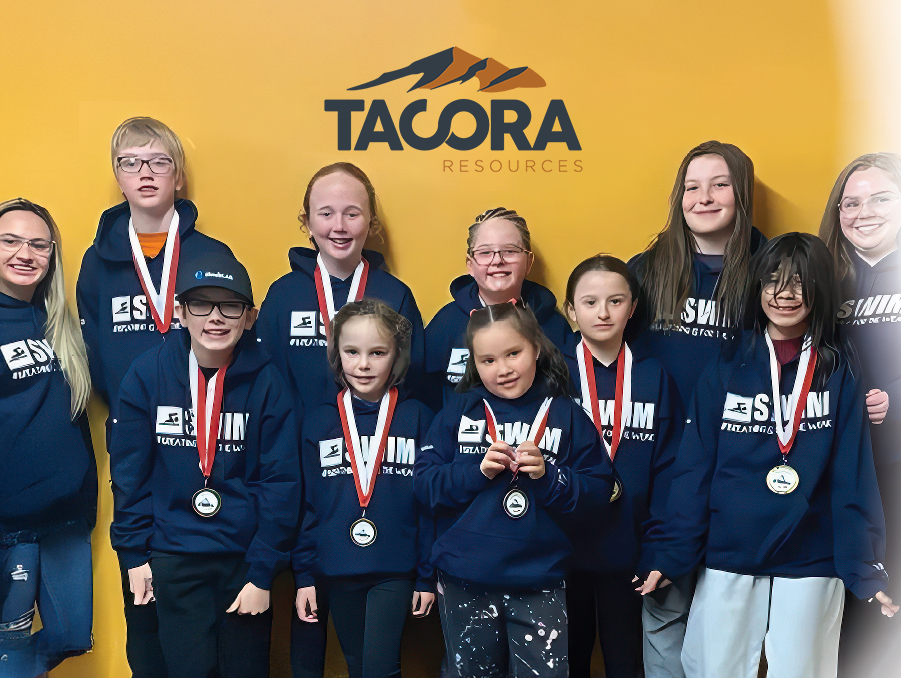
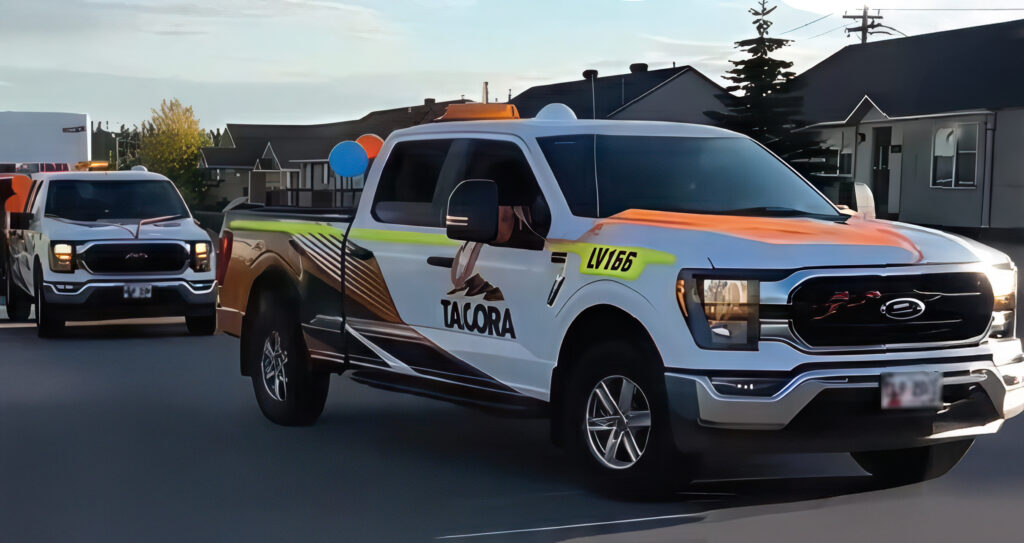
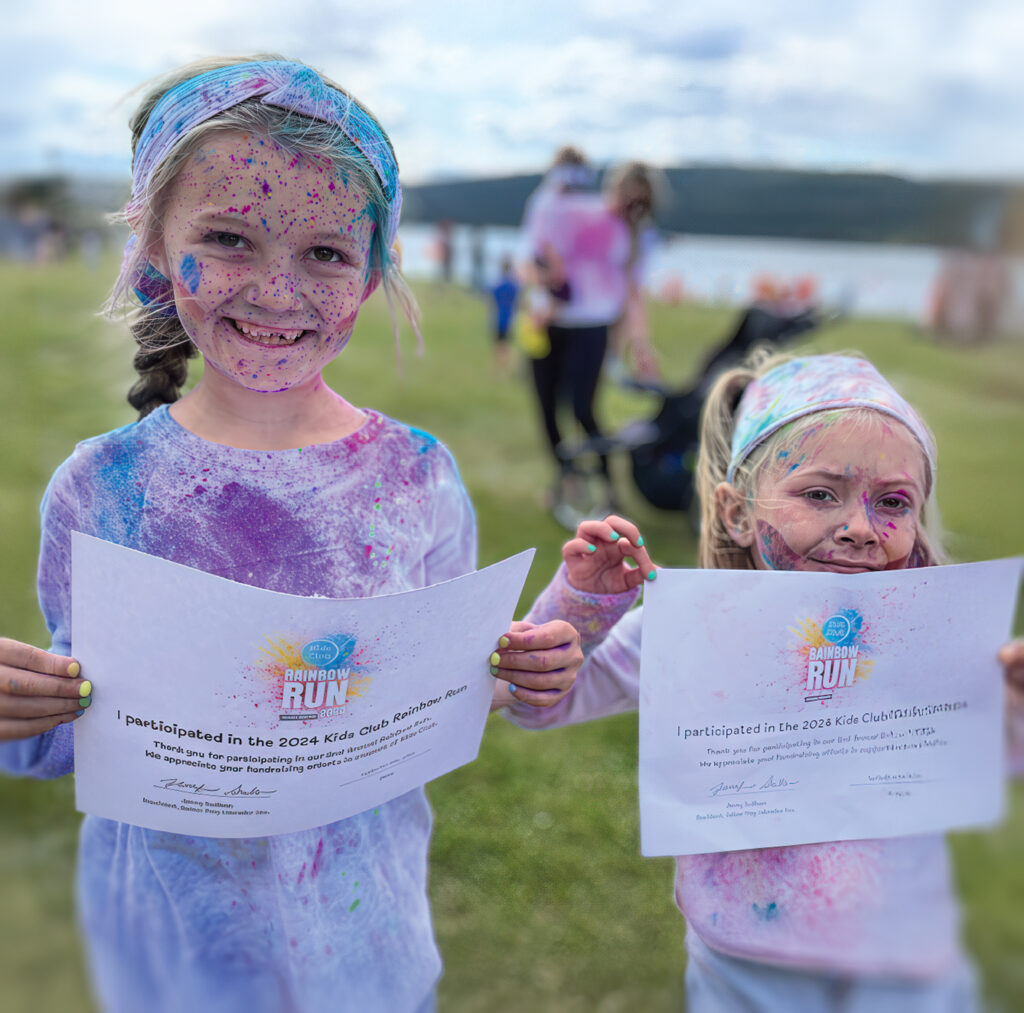
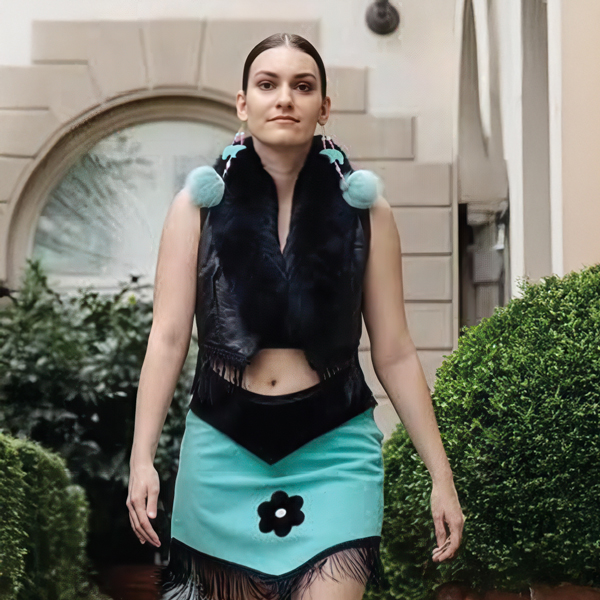
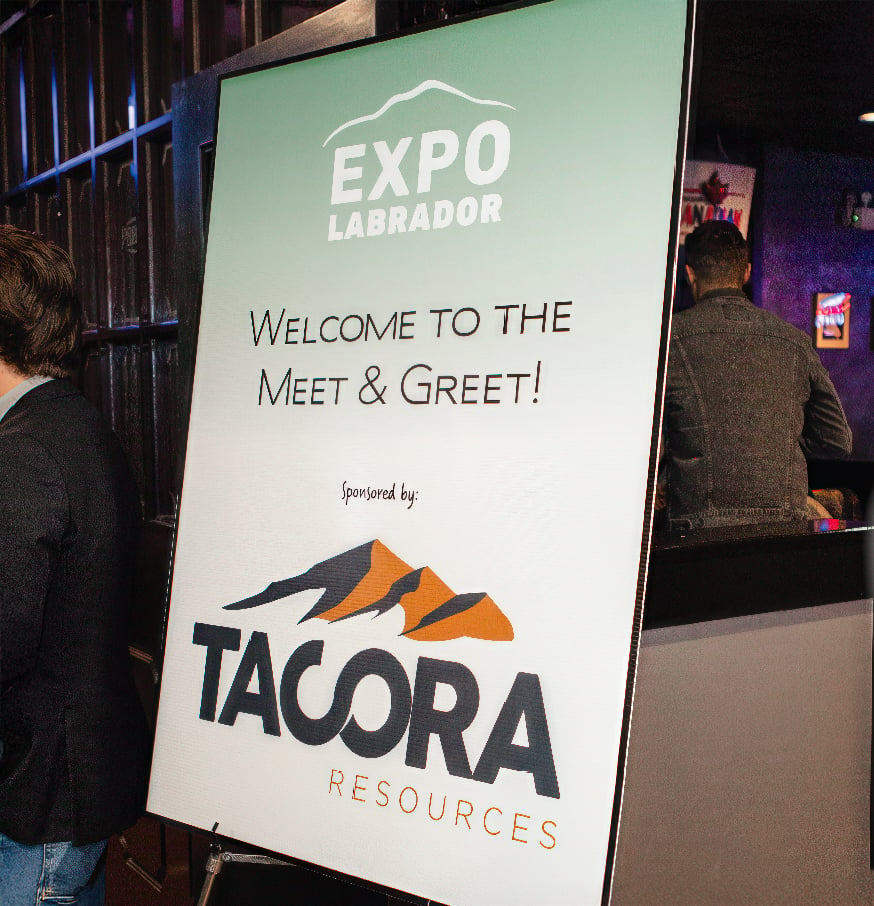
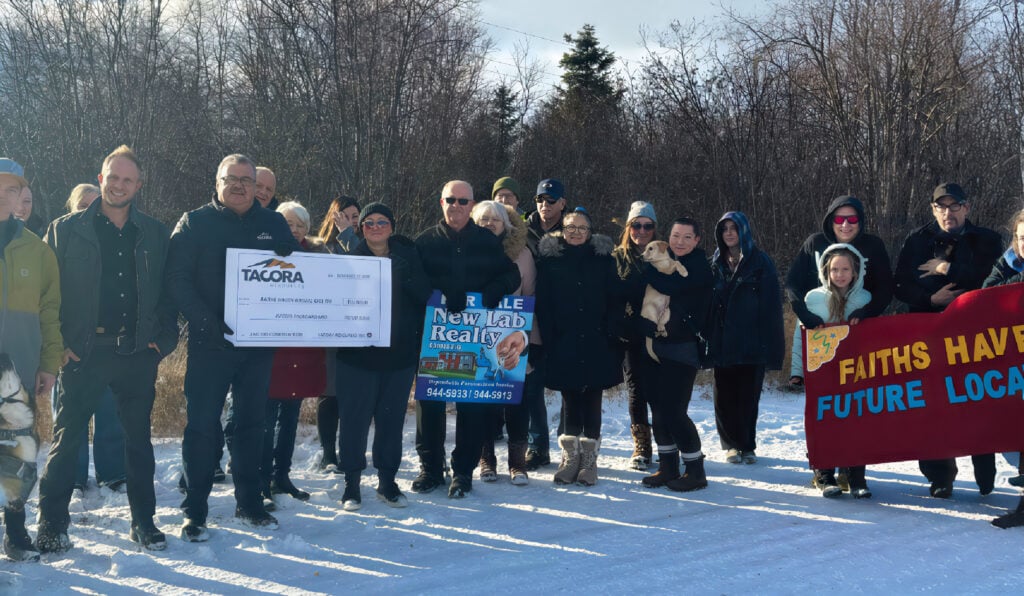
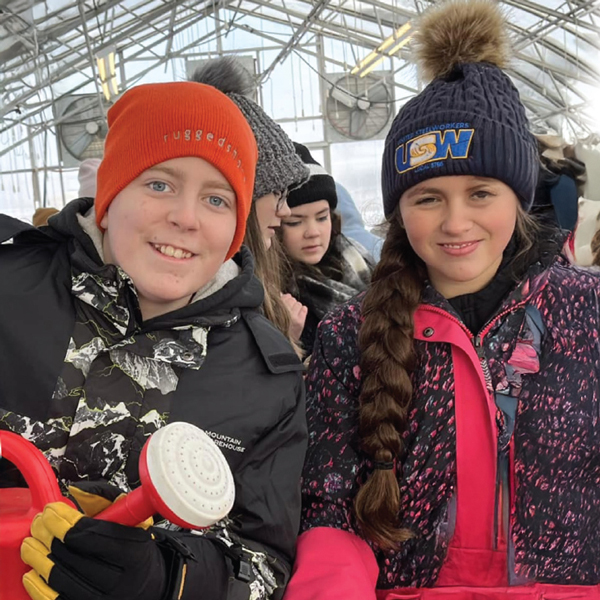
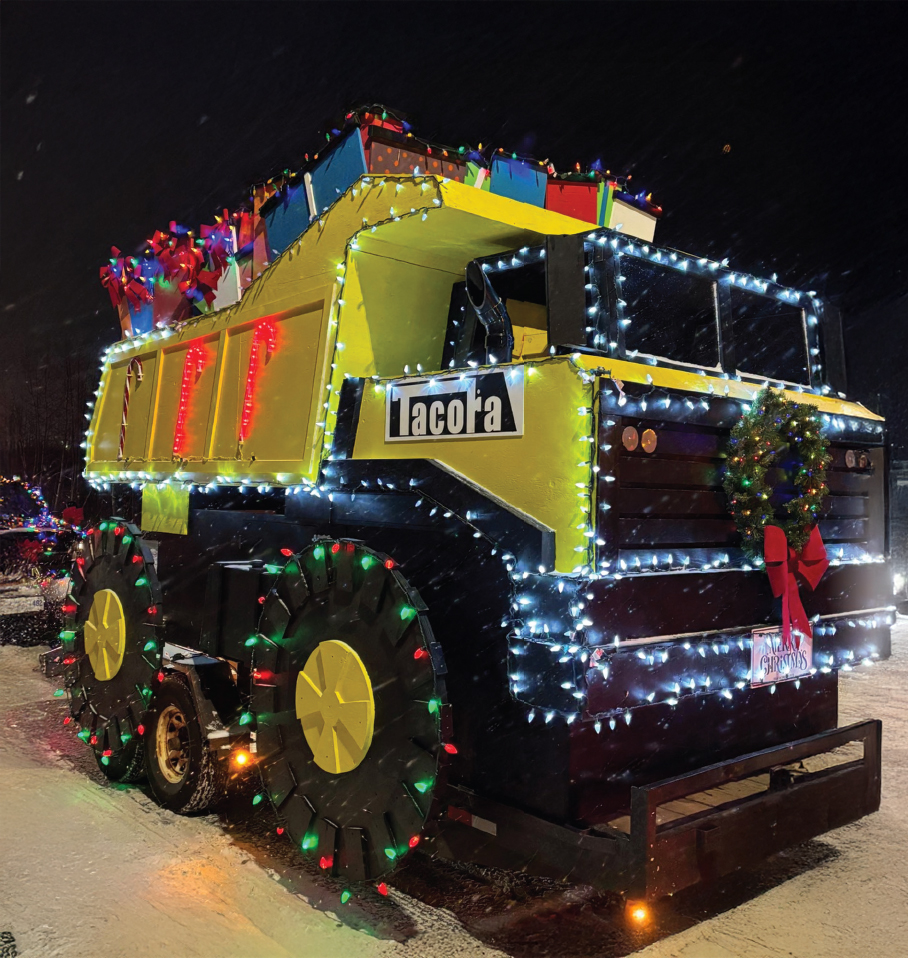
Tacora donated $5000.00 to the Salvation Army for their recent kitchen renovations. This will allow them to continue with their Outreach Ministry for the communities of Wabush and Labrador City.
Tacora Resources had the pleasure of transferring land to Faiths Haven Animal Shelter to help support Faiths Haven with their new facility for animals in need in our community.
In 2020, Tacora procured a total of $147,920,860 in goods and services. Of the $117,657,735 that was procured locally in Newfoundland and Labrador, $115,885,898 was directly procured within the Labrador region.
Tacora has a 3-year agreement with the Town of Wabush, whereby Tacora pays a grant-in-lieu of taxes to the town in the amount of $1.6 million per year. The agreement expires in 2022.
Tacora proudly presents the Adam Salomon de Friedberg Apprentice Scholarship Program, providing $3000 for new students entering 1st year into an apprentice trades program related to the mining industry, in memory of Adam Salomon De Friedberg.
Tacora also offers a āWomen in Miningā Trades Scholarship Award to encourage and support the growth of a diversified skilled mining workforce within the Labrador West region. These scholarships are available during each academic year.
Tacora has agreed, in partnership with the Town of Labrador City and the Iron Ore Company of Canada, to pay to the Town of Wabush a sum of $200,000 for three years (2019-2021).Ā
In 2020, Tacora procured a total of $147,920,860 in goods and services. Of the $117,657,735 that was procured locally in Newfoundland and Labrador, $115,885,898 was directly procured within the Labrador region.
Tacora has a 3-year agreement with the Town of Wabush, whereby Tacora pays a grant-in-lieu of taxes to the town in the amount of $1.6 million per year. The agreement expires in 2022.
Ā In 2021, TacoraĀ has donated to such groups as the Kids Club Indoor Playground, Menihek Nordic Ski Club, Encore Community Arts Association, Labrador West Salvation Army, Ronald McDonald House/Momma’s Dream Team, Wabush Fire Department, Labrador West Ground Search and Rescue, Ducks Unlimited and other non-profit organizations.
Tacora sponsored April Allen‘s debut at the Paris and Milan Fashion Weeks, showcasing a collection named “Arctic Elegance” that celebrates the beauty, resilience, and heritage of Inuit culture.
Tacora sponsored the Meet and Greet to kick off the 2024 Expo Labrador, providing opportunity for connection between fellow Labrador Businesses and Organizations.
Tacora is an active member of the Labrador West Chamber of Commerce.
Sydvaranger regularly consults with local politicians, environmental organizations, the Reindeer Grazing District 5AC Pasvik, the Sami Parliament and neighbors of the mining area.
Tacora Resources Community Giving Fund
Ā Tacora has established a Community Giving Fund to which community groups may apply for funding assistance.Ā All requests are assessed under a criteria matrix and each request is evaluated on an individual basis.
Local Impact
At Tacora, we recognize the importance in delivering economic benefits (direct and indirect) for the communities, businesses, and governments where we operate. Tacora supports the principles of first consideration and full and fair opportunity for suppliers located within the Province of NL, and works hard to create local impact wherever we operate.
We recognize that local employment is a primary benefit of our operations for local stakeholders, where 90% of Tacora employees are local and $34.2M directly procured within the Labrador Region. Through local employment, there are indirect impacts in stimulation of local economies, including demand for various local goods and services.Ā
Tacora commits to working with the province to identify trade shortages and implement training/apprenticeship programs in these areas. Educational opportunities and employee skill development are also offered by Tacora.
We believe in contributing to the prosperity and sustainability of our local and regional economies, and continue to invest in social, educational, environmental, and recreational programs that benefit local communities.
Indigenous Relations
Tacora recognizes the rich diversity of Indigenous Peoples who live in the region where we operate. We engage directly with Indigenous communities to foster meaningful and mutually beneficial relationships and seek to ensure our operations are respectful to Indigenous rights, cultural beliefs, and aspirations. We are committed to consulting with the five Indigenous Groups that claim traditional rights in Labrador West: Innu Nation of Labrador, Naskapi Nation of Kawawachikamach, Innu Nation of Matimekush-Lac John, Innu Nation of Takuaikan Uashat Mak Mani-Utenam, and NunatuKavut Community Council.
Tacora believes that participation from Indigenous Peoples ensure that a diverse range of perspectives, ideas, and local knowledge are considered in our operations. We facilitateĀ participation in a variety of ways, such as the Stakeholder Consultation Committee, Indigenous Partnership Agreements, permit review process, and ongoing communication through dedicate team members.
Stakeholder Consultation Committee
A Stakeholder Consultation Committee was established to facilitate the timely exchange of information and to provide an avenue for Tacora to receive feedback directly from communities. Participation in the Stakeholder Consultation Committee ensures representation from Indigenous Groups inĀ decision making, which helps align Tacoraās operations with community and cultural values, advancing sustainability and inclusivity.
Partnership agreements
Tacora has established a partnership agreement with Innu Nation and is working to implement agreements with the remaining groups. These agreements aim to ensure meaningful consultation and engagement on issues such as employment, business, environment and culture.
Reports & Policies
ESTMA Reports
ESTMA Reporting 2024
Download
ESTMA Reporting 2023
Download
ESTMA Reporting 2022
Download
ESTMA Reporting 2021
Download
ESTMA Reporting 2020
Download
ESTMA Reporting 2019
Download
Resource Sustainability Reports
Plans and Policies
Environmental Policy
Download
Health & Safety Policy
Download
2024 Modern Slavery Act
Download
2023 Modern Slavery Act
Download